The invention of injection molding has been a huge technological breakthrough during the 1800s. It was a discovery that led to many other technological developments in other industries because of the ability to create much more accurate plastic parts that would be used to create much more complex products. After the invention of the first injection molding machine in 1872 by the Hyatt brothers, the industry didn’t see a lot of technological advancement.
However, in 1983, the first all-electric machine was invented, finally bringing a different option for molders. Although, hydraulic type machines are still the most used ones around the world even though they are not as precise as other types.
But, this wasn’t the only technological advancement regarding the injection molding industry. In fact, there have been many advances that have brought us all kinds of benefits. We have seen improvement in durability, costs, reliability, structural integrity, and resistance in most products that are made through this process.
If I have piqued your interest in this subject, you will probably want to know about all the different tech advancements that happened over the year that pushed the injection molding industry to another level.
How does it work?
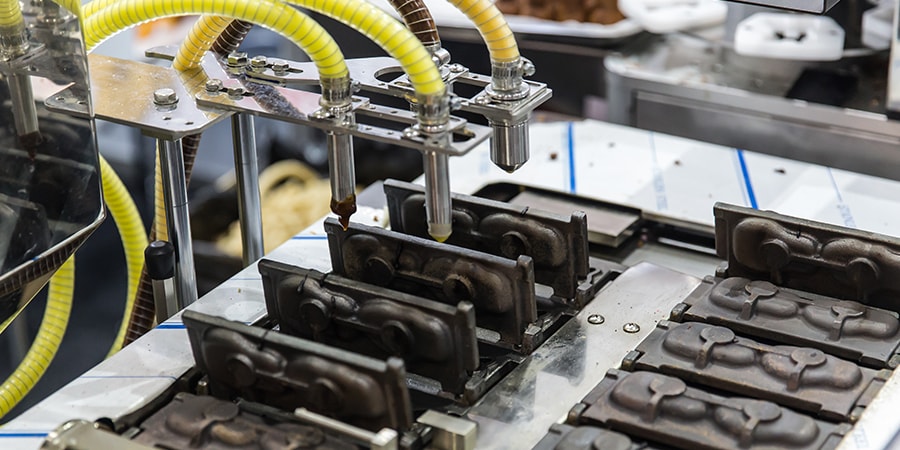
Source: blog.qad.com
Before we start explaining about all the different methods of injection molding, I should probably tell you about how it actually. Don’t worry, even though the machines that are used for this kind of manufacturing seem very complex and expensive, the process itself is actually very simple.
Certain material is melted until its state becomes liquid and then through different methods, that liquid is pushed into a mold. The most common material that companies use with this process is thermoplastic polymers. Keep in mind, that the material will differ depending on the machine. Some can handle basic polymer plastics, while some will be able to handle molten metal or even glass.
To be more specific, once the material used is made into molten liquid, a special nozzle is used to push it inside of the mold. It is very important that the pressure in the nozzle is high enough to fill every single part of the cavity of the die. Once the material cools down, the die can be removed and the product is ready to be used.
Thin-wall injection
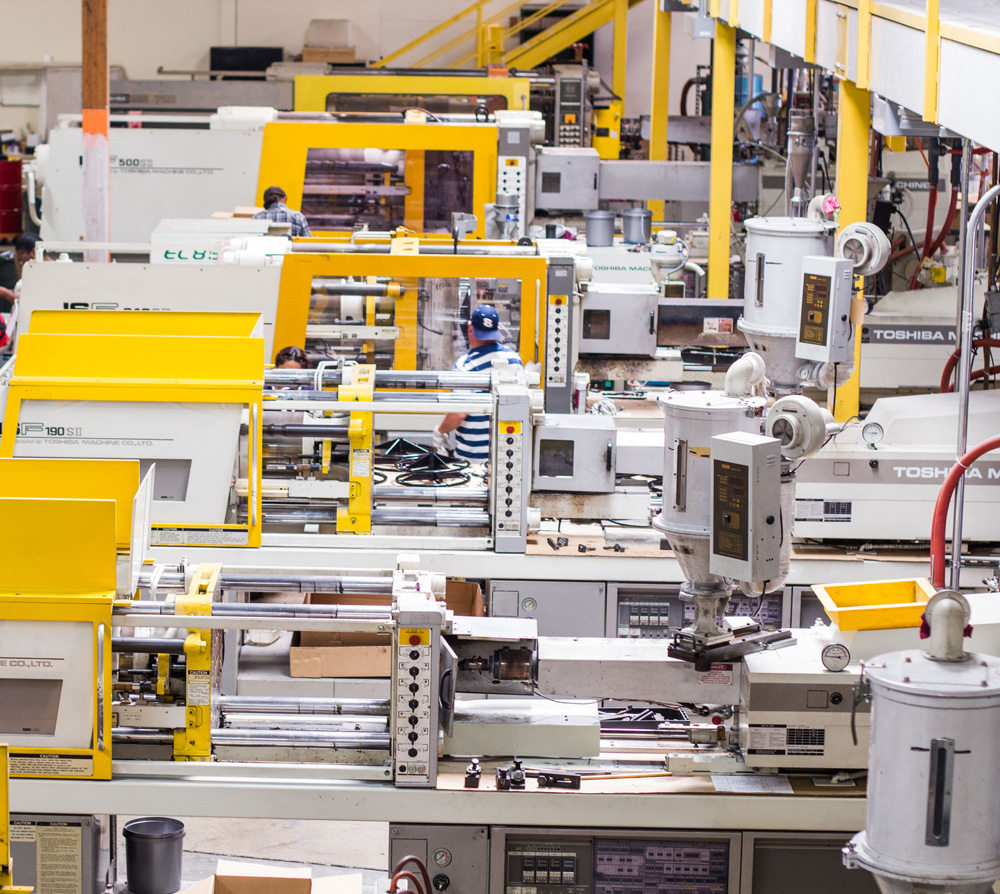
Source: damarplastics.com
This method is usually used for plastic parts that need to be mass-produced. The parts that come out of this process are usually very light and thin. In other words, it is used by companies to save a lot of money on material and on the cycle times. The machines are also less prone to breakage because the entire process is much simpler.
With the thin-wall method, companies can produce cheap and accurate plastic parts while they remain reliable enough to be used in other products. The consumption of thermoplastic polymer is reduced which can save a business a lot of money. Another benefit of thin-wall manufacturing is the low weight of the parts. Because of this shipping costs are much lower.
Thicker plastic parts also require much longer processing and manufacturing times, reducing the effectiveness of the factory. Last, but not least, is the fact that the emissions during this process are much lower. If you want to know more about all of the other methods used to inject plastic into a mold, you should check out qmolding.com. You could also check out their services if you have the need.
Microinjection

Source: syrmatech.com
This technological advancement is a bit more recent when comparing it to all of the other methods that are used throughout the industry. The market still hasn’t bloomed for microinjection, so finding companies will offer you this as an option is still quite rare.
However, this does not mean that the world does not have a need for this. In fact, if this were to become the world’s standard, products form injection molding would be much more durable and reliable. Today, with this method, parts are only made for very specialized products such as surgical equipment and other advanced medical tools. This equipment needs to be of the highest possible quality to ensure that the surgeries always go right. You could say that this technological advancement has saved many lives.
Automation
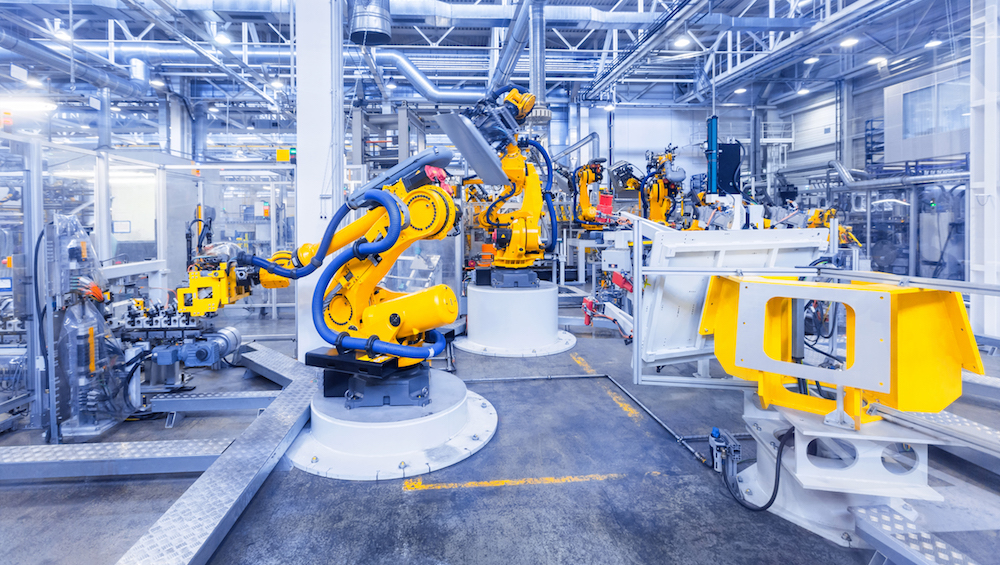
Source: gcenode.no
Just a couple of years, the injection molding industry couldn’t do anything without the right experts. Molders had to understand what to do from start to finish. Fortunately, with the world’s advancement in robotics, automation and artificial intelligence, parts of the injection molding can finally be automated. The use of robots in this industry will mean that the quality of most parts produced will be much higher and much more reliable. Human error has always been a problem, especially when creating intricate metal and plastic parts.
So, what does this exactly mean for most people’s daily lives? Well, it doesn’t exactly mean that anyone will feel a difference, but people would certainly notice that most of their products last much longer. Phones, vehicles, planes, boats, and many other different machines that we use every single day might last much longer and be much more reliable. Automation is definitely one of those technological advancements that will make a major change in the industry.
Faster computing
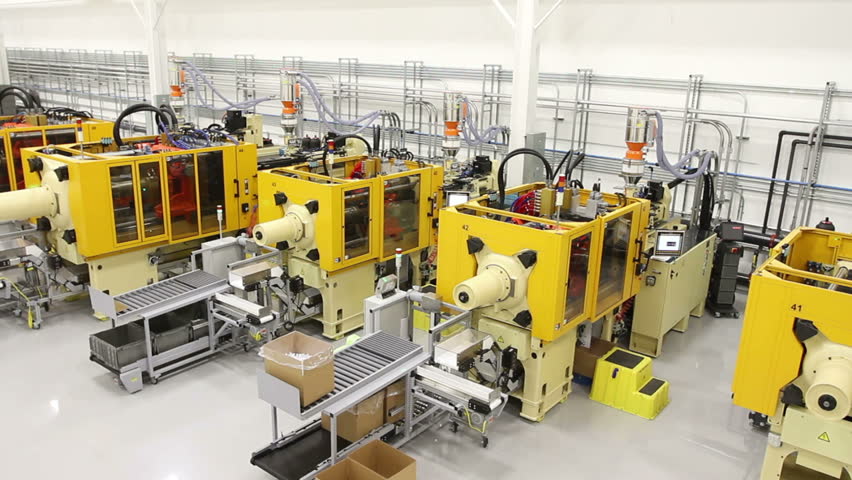
Source: shutterstock.com
Injection molding has become a process that creates much more accurate products that in the past. This change happened because of the world’s advancement of processors, RAM speed, etc. Most older machines in the industry use slow and old processors that can only create the most basic molding projections.
However, with today’s processors, the computers ni injection molding machines could be much more advanced and could do all kinds of tasks. The need for human operation and creativity might be completely removed.
All of these technological advancements have to lead us to much more high-quality products in every aspect of our lives. Cars, trains, and planes are safer, the phones in our pockets are much more durable and even the shoes that we were last longer than they used to.
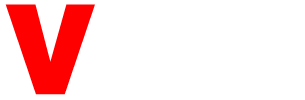